СССР
поковки ДЕТАЛЕЙ СОСУДОВ, АППАРАТОВ
И ТРУБОПРОВОДОВ ВЫСОКОГО ДАвленИЯ
Общие технические требования, правила
приемки, методы испытаний.
ОСТ 26-01-135-81
УТВЕРЖДЕН И ВВЕДЁН В ДЕЙСТВИЕ
приказом Всесоюзного промышленного объединения «Союзхиммаш»
30
сентября 1981 г. № 159
ИСПОЛНИТЕЛИ:
Г.Г. Золотенин, руководитель
темы
Т.П. Бурдуковская
Л.А. Корчагина
В.И. Этингов, канд. техн. наук
|
УТВЕРЖДЕНО
МИНИСТЕРСТВО
ХИМИЧЕСКОГО
И НЕФТЯНОГО МАШИНОСТРОЕНИЯ
Заместитель
Министра
П.Д.
Григорьев
30
сентября 1981 г.
|
ОТРАСЛЕВОЙ СТАНДАРТ
ПОКОВКИ
ДЕТАЛЕЙ СОСУДОВ, АППАРАТОВ И ДЕТАЛЕЙ ТРУБОПРОВОДОВ ВЫСОКОГО ДАВЛЕНИЯ.
Общие технические требования,
правила приемки, методы испытаний.
|
ОСТ 26-01-135-81
Взамен
ОСТ 26-1365-75
|
Приказом Всесоюзного
промышленного объединения от 30 сентября 1981 г. № 159 срок действия
с
01.07.1982 г.
до
01.01.1992 г.
(Измененная редакция, Изм. № 2).
Несоблюдение
стандарта преследуется по закону
Настоящий стандарт распространяется на поковки цельнокованых корпусов,
обечаек, патрубков, уплотнительных колец двухконусного и треугольного сечения с
толщиной стенки до 300 мм, плоских и штампуемых днищ и крышек, трубных досок,
фланцев, горловин сечением до 800 мм для сосудов на рабочую температуру от
минус 40 до плюс 420 °С и давление св. 10 до 130 МПа (св. 100 до 1300 кгс/см2)
и поковки деталей трубопроводов на рабочую температуру от минус 50 до плюс 510
°С, работающих под давлением св. 10 до 100 МПа (св. 100 до 1000 кгс/см2).
(Измененная редакция, Изм. № 2).
Стандарт соответствует СТ СЭВ
1326-78 (в части требований к поковкам).
1.1. Поковки должны изготовляться в соответствии с требованиями
настоящего стандарта по рабочей документации, утвержденной в установленном
порядке.
1.2. Для изготовления поковок должны применяться качественные
углеродистые, низколегированные, легированные и высоколегированные стали,
выплавленные в мартеновских и электрических печах.
Допускается выплавка стали
методами ВДП и ЭШП и обработка металла на установке УВРВ-АSlА или РН.
1.3. Марка стали поковок, условия применения и назначения должны
соответствовать обязательному приложению 1.
Температурные границы применения
сталей установлены в соответствии с Правилами Госгортехнадзора:
для деталей сосудов - «Правилами
устройства и безопасной эксплуатации сосудов, работающих под давлением»;
для деталей трубопроводов -
ПУГ-69 «Правилами устройства и безопасной эксплуатации трубопроводов для
горючих, токсичных и сжиженных газов», нормативно-технической документацией на
соответствующие виды изделий без учета коррозионного воздействия сред.
Условия применения сталей в
коррозионных средах, содержащих водород, окись углерода, аммиак, должны
устанавливаться в соответствии с обязательным приложением 2.
1.4. По согласованию с
ИркутскНИИхиммашем могут применяться другие материалы или материалы, указанные в
настоящем документе, на другие параметры в пределах, установленных
Гостехнадзором СССР.
(Новая редакция, Изм. № 2).
1.5. По химическому составу стали, применяемые для изготовления
поковок, должны удовлетворять требованиям государственных стандартов и технических
условий.
1.6. Поковки должны изготовляться из слитков, кованых и катаных
заготовок по технологии, принятой на заводе-изготовителе, обеспечивающей
требования рабочей документации и настоящего стандарта.
В случае изготовления нескольких
деталей из одной поковки результаты контрольных испытаний распространяются на
все детали.
(Измененная редакция, Изм. № 1).
1.7. Форма и размеры поковок должны соответствовать рабочей
документации на готовую деталь, с учетом припусков на механическую обработку и
вырезку проб, допусков на точность изготовления, установленных ГОСТ
7829-70 и ГОСТ
7062-79.
Для поковок из высоколегированной стали, для поковок из слитков,
отлитых в вакууме, припуски и напуски устанавливаются документацией
завода-изготовителя.
(Измененная редакция, Изм. № 1).
1.8. На поверхностях ножовок, не
подвергающихся механической обработке, не допускаются дефекты, выходящие за
пределы допусков на поковку.
На обрабатываемых поверхностях
поковок могут быть допущены заковы, плены, песочины, раковины, если их глубина
не более 75 % фактического одностороннего припуска на механическую обработку.
При глубине поверхностных
дефектов, превышающих припуск на механическую обработку, допускается удаление
дефектов пологой вырубкой с последующей заваркой и термической обработкой.
Глубина поверхностных дефектов определяется вырубкой. Допускаемая глубина
заварки должна быть согласована с заказчиком и ИркутскНИИхиммашем. Полноту
удаления дефектов под заварку допускается проверять магнитопорошковым и цветным
методом.
1.9. На механически обработанных поверхностях
поковок не допускаются трещины, заковы, плены, раковины любых размеров.
(Измененная редакция, Изм. № 1).
1.10. В рабочей документации на поковки завода-изготовителя должны быть
указаны места вырезки проб всех видов испытаний, предусмотренных настоящим
стандартом, а также поверхности для ультразвукового контроля.
1.11. По результатам ультразвукового метода контроля в поковках не
допускаются следующие дефекты:
отдельные непротяженные эквивалентной площадью от S0 мм2 до S1 мм2
включительно в количестве, превышающем нормы, указанные в табл. 1 и 2;
протяженные, превышающие
условную протяженность искусственного отражателя площадью S1 мм2 при чувствительности контроля S0 мм2;
отдельные непротяженные
эквивалентной площадью свыше S1 мм2 (табл.
1)
до S2 = 50
мм2 в количестве более 2-х, на участке площадью В0 = 0,09
м2 (0,3 м ´ 0,3
м) и более 3-х на участке В1 = 1 м2, если
пространственное (объемное) расстояние между ними менее 50 мм при толщине
поковки свыше 250 мм (только для углеродистых, низколегированных и легированных
сталей).
1.12. Окончательная термическая обработка должна производиться после
предварительной механической обработки.
По усмотрению
завода-изготовителя допускается производить окончательную термическую обработку
без предварительной механической обработки. Виды термической обработки
приведены в справочном приложении 3.
(Измененная редакция, Изм. № 1).
1.13. Сегрегация серы при контроле макроструктуры поковок не должна
превышать 3 балл по шкале Новокрамоторского машиностроительного завода для
соответствующего развеса слитков.
При получении серного отпечатка четвертого балла вопрос о годности
поковок определяется по согласованию между Заказчиком и Поставщиком при условии
удовлетворительных результатов остальных испытаний и контроля, предусмотренного
настоящим стандартом.
При контроле макроструктуры на травленой поверхности поковок или
вырезанных проб не должно быть трещин, флокенов, рыхлостей, усадочных раковин.
Места повышенной травимости не являются браковочными признаками.
(Измененная редакция, Изм. № 1).
1.14. При наличии требований заказчика поковки из аустенитных сталей до
запуска в производство независимо от наличия сертификата, должны быть проверены
на склонность к межкристаллитной коррозии.
1.15. Загрязненность металла поковок деталей трубопроводов оксидами,
силикатами и сульфидами не должна превышать средний балл 3,5, максимальный балл
для силикатов и оксидов 5 и 4 балл для сульфидов по требованию чертежа, согласованному с изготовителем.
(Измененная редакция, Изм. № 1).
1.16. Маркировка должна быть четко выбита на каждой поковке со стороны
прибыльной части слитка и должна содержать:
номер чертежа,
марку стали,
номер поковки,
номер плавки,
для деталей трубопроводов Ду
от 6 до 200 мм:
номер чертежа,
марку стали,
номер плавки.
Таблица 1
Оценка
качества поковок по результатам ультразвукового метода контроля для
углеродистых, низколегированных, легированных сталей, вакуумированной стали 22К
Масса
необработанной поковки, т
|
Толщина поковки, мм
|
Минимальная фиксируемая эквивалентная площадь дефекта, S0, мм2
|
Недопустимые дефекты,
эквивалентной площадью S1, мм2, свыше
|
Недопустимое количество
дефектов, свыше
|
на участке В0 =
0,09 м2
|
на участке В1 = 1 м2
|
n0, шт.
|
n1, шт.
|
Прямой преобразователь
|
до
12
|
до
30
св.
30 до 40
св.
40 до 250
св.
250 до 500
св.
500
|
5
5
5
7
10
|
5
7
10
15
20
|
3
5
10
20
30
|
-
-
20
40
40
|
св.
12 до 30
|
до
250
св.
250 до 500
св.
500
|
7
10
10
|
15
20
25
|
20
20
30
|
40
40
60
|
св. 30 до 85
|
до
500
св.
500
|
15
|
30
|
20
30
|
40
60
|
Наклонный преобразователь
|
Любая
|
до
30
св.
30 до 70
св.
70 до 150
св.
150 до 200
св.
200
|
3
3
5
10
20
|
5
5
7
20
30
|
3
5
10
15
20
|
-
-
15
20
30
|
Примечание. Суммарное количество дефектов,
выявляемых прямым и наклонным преобразователями, не должно превышать
количество дефектов, выявляемых прямым преобразователем, указанным в таблице.
|
Таблица 2
Оценка
качества поковок по результатам ультразвукового метода контроля для аустенитных
сталей
Толщина
поковки,
мм
|
Минимальная фиксируемая эквивалентная площадь, S0, мм2
|
Недопустимые дефекты,
эквивалентной площадью S1, мм2, свыше
|
Недопустимое количество дефектов,
свыше
|
на участке В0 =
0,09 м2 (0,3 м × 0,3 м)
n0, шт.
|
на участке В1 = 1 м2
n1, шт.
|
Прямой преобразователь
|
до
30
|
5
|
7
|
1
|
-
|
св.
30 до 40
|
10
|
20
|
3
|
-
|
св.
40 до 250
|
10
|
20
|
5
|
10
|
св.
250 до 500
|
20
|
40
|
5
|
10
|
св.
500
|
40
|
60
|
5
|
10
|
Наклонный преобразователь
|
до
30
|
10
|
10
|
1
|
-
|
св.
30 до 70
|
10
|
20
|
3
|
5
|
св.
70 до 150
|
10
|
20
|
5
|
10
|
св.
150 до 200
|
20
|
40
|
5
|
10
|
св.
200
|
40
|
60
|
5
|
10
|
Примечание. Суммарное количество
дефектов, выявленных прямым и наклонным преобразователями, не должно
превышать количество дефектов, выявленных прямым преобразователем, указанным
в таблице.
|
Для мелких
поковок допускается маркировка на бирках. Принятая поковка заверяется клеймом
ОТК завода-изготовителя. Место маркировки обводится цветной несмываемой
краской. После проведения предварительной механической обработки поковок
маркировка восстанавливается. Правильность маркировки заверяется клеймом ОТК.
2.1. Приемка поковок
производится в соответствии с требованиями настоящего стандарта и чертежей
поковок на основании:
химического анализа (по плавочной пробе);
внешнего осмотра, проверки размеров и маркировки;
магнитной и цветной дефектоскопии (при необходимости);
ультразвуковой дефектоскопии;
контроля макроструктуры;
механических испытаний, замера твердости;
для аустенитных сталей контроля на стойкость к МКК при наличии требований
Заказчика.
Группа IV и V и определение партии устанавливается в
соответствии с ГОСТ
8479-70 и определяется технической документацией на изделие.
(Новая редакция, Изм. № 1).
2.2. Виды и объем испытаний должны соответствовать табл. 3.
2.3. Каждая поковка до и после предварительной механической обработки должна
подвергаться внешнему осмотру для выявления поверхностных дефектов и
возможности их исправления в соответствии с п.п. 1.8. и 1.9.
2.4. Магнитопорошковая
или цветная дефектоскопия проводится выборочно в тех местах, где внешним
осмотром обнаружены дефекты, а также в местах исправления наружных дефектов.
Магнитопорошковая и цветная дефектоскопия производится по технической
документации, утвержденной в установленном порядке.
(Новая редакция, Изм. № 1).
2.5. Ультразвуковая дефектоскопия должна проводиться после
предварительной механической обработки, окончательной термической обработки,
контроля внешним осмотром или магнитопорошковой дефектоскопии.
2.6. Цельнокованые корпуса, обечайки проверяются на однородность по
твердости через каждые 3 м длины в трех местах по окружности через 120°. При этом твердость в любой точке должна находиться
в пределах, указанных в обязательном приложении 4.
Замер твердости допускается проводить прибором Польди.
2.7. Механические свойства поковок на тангенциальных образцах после
окончательной термической обработки должны удовлетворять требованиям,
приведенным в обязательном приложении 4.
Механические свойства при
повышенных температурах должны удовлетворять требованиям, приведенным в
обязательном приложении 5.
Таблица 3
Виды и
объемы испытаний
Наименование
детали
|
Химический анализ
|
Внешний осмотр, проверка
размеров и маркировка
|
Магнитопорошковый или цветной
метод контроля
|
Ультразвуковой метод контроля
|
Макроисследование
|
Испытание на твердость
|
Испытание на растяжение и
ударную вязкость
|
Количество образцов от пробы
|
Испытание на межкристаллитную
коррозию
|
Контроль загрязненности
неметаллическими включениями
|
на растяжение
|
на ударную вязкость
|
Детали
сосудов
|
Каждая
плавка
|
Каждая
поковка
|
Выборочно
в местах, где внешним осмотром обнаружены дефекты, а также в местах
исправления поверхностных дефектов
|
Каждая
поковка
|
Каждая
поковка
|
Каждая
поковка кроме поковок из аустенитных сталей
|
Объем испытаний
определяется группой IV или V по ГОСТ 8479-70 на основании технической документации на изделие
|
1
|
2
|
Каждая
поковка из аустенитной стали
|
Не
проводится
|
Детали
трубопроводов с условным проходом от 250 до 400 мм
|
Детали
трубопроводов с условным проходом от 6 до 200 мм
|
Каждая
поковка деталей Ду = 32 мм и выше, кроме поковок из аустенитных
сталей
|
Не
проводится
|
1 % поковок, но не менее 2
шт. от партии с крайними значениями твердости, указанными в приложении 4
|
Поковки
из аустенитной стали, одна поковка от
партии-садки. Допускается контроль МКК производить от плавки на плавочной
пробе
|
Каждая
плавка
|
Уплотнительные
кольца двухконусные и треугольного сечения
|
Каждая
поковка
|
Не
проводится
|
Не
проводится
|
Не
проводится
|
Каждая
поковка из аустенитной стали
|
Не
проводится
|
(Измененная
редакция, Изм. № 1, 2).
Температура испытаний
указывается в технической документации. По соглашению с заказчиком определение
механических свойств при повышенных температурах можно не производить, если
изготовитель гарантирует соответствие характеристик установленным нормам.
3.1. Отбор проб для определения химического состава металла
производится по ГОСТ
7565-73.
3.2. Химический анализ металла поковок должен производиться по ГОСТ
12344-78 ÷ ГОСТ
12365-84.
(Измененная редакция, Изм. № 2).
При изготовлении поковок из
металла, выплавляемого предприятиями изготовителями, химический состав стали
определяется по плавочному анализу ковшевой пробы.
При изготовлении поковок из
проката марка стали и химический состав устанавливается по сертификату
металлургического предприятия.
3.3. Внешний осмотр, цветной и магнитопорошковый методы дефектоскопии
следует проводить в соответствии с требованиями ГОСТ 3342-79, ГОСТ
18442-80 и ГОСТ 21105-75 соответственно
и действующей технической документацией, утвержденной в установленном порядке.
3.4. Ультразвуковой метод дефектоскопии следует проводить в
соответствии с требованиями настоящего стандарта, ГОСТ
24507-80, по действующей нормативно-технической документации, утвержденной
в установленном порядке.
3.5. Поверхности поковок, со стороны которых производится цветной и
магнитопорошковый методы дефектоскопии не должны иметь шероховатость более Rz 40, а для проведения ультразвукового метода
дефектоскопии более Rz 10 по ГОСТ 2789-73
(СТ СЭВ 638-77).
Поверхности поковок,
параллельные поверхностям ввода ультразвуковых колебаний (донные поверхности),
не должны иметь шероховатость более Rz 40.
(Измененная редакция, Изм. № 2).
3.6. Ультразвуковому методу дефектоскопии должно подвергаться 100 %
объема каждой поковки.
3.7. При отсутствии
донного эхо-сигнала или невозможности контроля с чувствительностью S0 вопрос о годности поковки решается между Поставщиком и Заказчиком.
(Новая редакция, Изм. № 1).
3.8. Контроль макроструктуры на снятие серии отпечатков поковок длиной
более 5 м должен производиться с двух сторон.
При контроле макроструктуры поковки не должны иметь флокенов, трещин, усадочной
рыхлости. Величина отброса должна быть не менее 50 мм. Контроль макроструктуры
металла проводится на следующих участках поковок:
для пустотелых поковок и плоских днищ с отбортовкой - при наружном
диаметре свыше 2000 мм на трех темплетах, расположенных под углом 120° по периметру поковки. Длина каждого должна
быть не менее 400 мм, ширина темплета - равна толщине поковки;
для сплошных поковок на торцах поковок по двум взаимноперпендикулярным
полосам шириной 150 - 200 мм, проходящим через центр;
для поковок (плит) поперек направления волокон из средней трети по
ширине.
Площадь поперечного сечения темплета должна быть не менее произведения
толщины поковки на ширину темплета (не менее 150 мм). При толщине поковки свыше
300 мм допускается разрезка темплета на две или три части по толщине.
В случае обнаружения дефектов, контроль следует производить по всей
поверхности.
(Измененная редакция, Изм. № 1, 2).
3.9. Снятие серных отпечатков должно производиться на полосе шириной не
менее 150 мм на следующих участках поковок:
для пустотелых кольцевых поковок
и плоских днищ с отбортовкой - на открытых торцах, при длине поковки до 5 м со
стороны прибыльной части, при длине более 5 м с двух диаметрально
противоположных сторон по сечению;
для сплошных поковок (крышки, днища)
- на одном из торцев поковки.
3.10. Механические свойства поковок должны определяться на
тангенциальных и поперечных (при изготовлении крышек из ковано-катаных плит)
образцах.
3.11. Вырезка проб для механических испытаний поковок деталей сосудов
должна производиться согласно табл. 4.
3.12. Размеры напуска на пробы должны быть достаточными для
изготовления необходимого количества образцов с учетом возможности проведения
повторных испытаний.
3.13. Из пустотелых и
рассверленных поковок с толщиной стенки до 100 мм образцы вырезают на
расстоянии одной второй толщины стенки поковки, а при толщине свыше 100 мм - на
расстоянии одной трети толщины стенки поковки от поверхности.
(Новая редакция, Изм. № 1).
3.14. Образцы для механических испытаний поковок цилиндрической и
призматической формы вырезают из напуска или тела поковок. Ось образца должна находиться на расстоянии
одной трети радиуса или одной шестой диагонали от наружной поверхности поковки. Для поковки типа плиты пробы вырезаются из
средней трети по ширине.
Допускается вырезать:
от крышек - поперечные образцы в местах расположения отверстий под
основные шпильки или входные патрубки (проба 2, табл. 4). В этом случае уровень
механических свойств устанавливается по соглашению сторон.
(Измененная редакция, Изм. № 1, 2).
3.15. Образцы для механических испытаний поковок деталей
трубопроводов должны вырезаться из запусков для проб, из тела поковки или отдельной
пробы для поковок массой до 150 кг из металла той же плавки, такого или
большего сечения, прошедшей те же технологические операции и термически
обработанные совместно с поковками данной партии.
Отрезка проб и вырезка заготовок
для образцов должны проводиться в тангенциальном направлении. Оси образцов
должны находиться в центре толщины стенки поковки.
Размеры напуска должны
обеспечивать возможность вырезки необходимого количества образцов с учетом
возможности проведения повторных испытаний.
Таблица 4
Схема
отбора проб для деталей сосудов
Вид
поковки
|
Место вырезки проб
|
Порядок вырезки проб
|
Поковка
корпуса
|
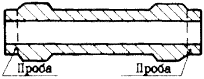
|
При
длине корпуса до 3 м, а также для корпуса с глухим днищем, пробы вырезаются с
одного конца, соответствующего верху слитка. При длине корпуса более 3 м - с
двух концов.
|
Поковка
обечайки с фланцем
|
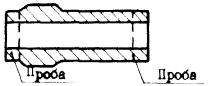
|
При
длине обечайки с фланцем до 3 м проба вырезается с одного конца,
соответствующего верху слитка. При длине обечайки с фланцем более 3 м - с
двух концов.
|
Поковка
обечайки
|
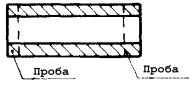
|
При
длине обечайки до 3 м пробы вырезаются с одного конца, соответствующего верху
слитка, при длине обечайки более 3 м - с двух концов.
|
Поковка
днища, горловины,
фланца, патрубка
|
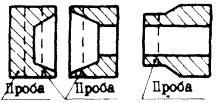
|
Допускается
пробу отрезать от глухого конца днища.
|
Поковка
крышки трубной доски, плиты для штампованных днищ и крышек (ковано-катаная)
|
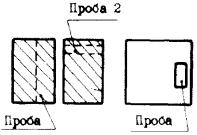
|
Пробу
2 вырезать пустотелым сверлом в местах расположения на детали отверстия под основные
шпильки или входные и выходные патрубки. В этом случае образцы вырезаются
вдоль оси пробы.
|
Поковка крышки из
ковано-катаной плиты
|
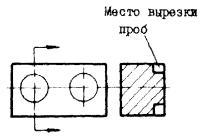
|
Тангенциальные образцы,
ось которых должна быть не менее 60 мм от наружной поверхности
|
(Измененная редакция,
Изм. № 1).
3.16. Вырезка проб и изготовление образцов должны осуществляться
методами, не изменяющими микроструктуру металла и его механических свойств.
3.17. Количество образцов для механических испытаний должно
соответствовать табл. 3.
3.18. Испытание на растяжение производится по ГОСТ 1497-84.
(Измененная редакция, Изм. № 2).
3.19. Испытание на ударную вязкость производится по ГОСТ
9454-78 (СТ СЭВ 472-77, СТ
СЭВ 473-77), образец тип 1.
(Измененная редакция, Изм. № 2).
3.20. Значение ударной вязкости при температуре минус 40 °С не должно быть менее 200 кДж/м2
(2,0 кгс·м/см2). Определение ударной вязкости при температуре минус
40 °С допускается не
проводить, если изготовитель гарантирует соответствие ударной вязкости
установленным нормам.
(Измененная редакция, Изм. № 1).
3.21. Испытание на твердость по Бринеллю производится по ГОСТ
9012-69 (СТ СЭВ 468-77). Допускается контроль твердости производить
прибором Польди по методике завода-изготовителя.
Замер твердости разрешается производить на головках разрывных или
ударных образцов.
(Измененная редакция, Изм. № 1, 2).
3.22. При получении неудовлетворительных результатов хотя бы на одном из
образцов допускается проводить повторные испытания на удвоенном количестве
образцов, взятых от той же пробы, для того вида испытаний, который показал
неудовлетворительные результаты.
При неудовлетворительных
результатах повторных испытаний поковки должны быть подвергнуты повторной
термической обработке.
3.23. Число термических обработок не должно быть более трех.
Дополнительный отпуск не считается повторной термической обработкой.
После каждой термической
обработки поковки предъявляются к сдаче как при первом предъявлении.
3.24. Загрязненность металла неметаллическими включениями определяют по
ГОСТ
1778-70 (СТ СЭВ 4077-83), методом III-1.
(Измененная редакция, Изм. № 2).
3.25. Испытание на склонность к межкристаллитной коррозии производится
по ГОСТ
6032-84 (СТ СЭВ 4076-83), методом АМ иди АМУ.
При получении
неудовлетворительных результатов контроля на МКК поковки должны подвергаться
повторной термической обработке.
(Измененная редакция, Изм. № 2).
3.26. Для контроля проверки заказчиком качества поковок и соответствия
их требованиям настоящего стандарта должны применяться правила отбора проб и
методы испытаний, установленные настоящим стандартом.
ПРИЛОЖЕНИЕ 1
Обязательное
Таблица
Марка
стали
|
Стандарт
или технические условия
|
Рабочая
температура стенки, °С
|
Назначение
|
20
|
ГОСТ
1050-74
|
От минус 30 до плюс 380
|
Детали сосудов
|
от
минус 40 до плюс 450
|
Детали трубопроводов Ду 6
- 200 мм
|
22К
|
по
настоящему стандарту
|
От минус 30 до плюс 380
|
Детали сосудов
|
15ГС
|
ОСТ 108.030.113-77
|
От минус 40 до плюс 400
|
Детали трубопроводов Ду 6
- 200 мм
|
09Г2С
14ХГС
|
ГОСТ
19282-73
|
От минус 40 до плюс 380
|
Детали сосудов
|
14ХГС
|
От минус 40 до плюс 250
|
Детали трубопроводов Ду
250 - 400 мм
|
От минус 50 до плюс 400
|
Детали трубопроводов Ду 6
- 200 мм
|
30ХМА
|
ГОСТ
4543-71
|
От минус 40 до плюс 420
|
Детали сосудов
|
От минус 50 до плюс 475
|
Детали трубопроводов Ду 6
- 200 мм
|
20Х2МА
|
По настоящему стандарту
|
От минус 40 до плюс 475
|
Детали трубопроводов Ду 6
- 200 мм
|
От
минус 40 до плюс 350
|
Детали трубопроводов Ду
250 - 400 мм
|
22Х3М
|
ТУ 108-838-75
|
От минус 40 до плюс 420
|
Детали сосудов
|
от минус 40 до плюс 475
|
Детали трубопроводов Ду 6
- 200 мм
|
от
минус 40 до плюс 350
|
Детали трубопроводов Ду
250 - 400 мм
|
15Х2МФА
(48ТС-3-40)
18Х2МФА
(48ТС-3)
|
ТУ
108-131-75
|
От 0 до плюс 420
|
Детали сосудов
|
25Х2МФА
(48ТС-1)
25Х3МФА
(43ТС-4)
|
Несвариваемые детали сосудов
|
18Х3МВ
|
ГОСТ 20072-74
|
От минус 40 до плюс 420
|
Несвариваемые детали сосудов
|
От минус 50 до плюс 475
|
Несвариваемые детали трубопроводов Ду
6 - 200 мм
|
20Х3МВФ
|
От минус 50 до плюс 510
|
38ХН3МФА
|
ГОСТ
4543-71
|
От минус 40 до плюс 420
|
Несвариваемые детали сосудов
|
08X13
12X13
20X13
30X13
|
ГОСТ
5632-72
|
От минус 40 до плюс 420
|
Детали сосудов
|
12Х18Н10Т
|
ГОСТ
5632-72
|
От минус 40 до плюс 420
|
Детали сосудов
|
12Х18Н10Т
10Х17Н13М2Т
10Х17Н13М3Т
08Х17Н15М3Т
|
От минус 50 до плюс 510
|
Детали трубопроводов Ду 6
- 200 мм
|
16ГС
|
ГОСТ
19282-73
|
от
минус 20 до плюс 380
|
детали
сосудов и детали трубопроводов Ду 6 - 200 мм
|
15Х5М
|
ГОСТ
20072-74
|
от
минус 40 до плюс 510
|
(Измененная
редакция, Изм. № 2).
Обязательное
Таблица 1
Максимально допустимая температура применения
сталей в водородосодержащих средах (°С)
Марка стали
|
Парциальное давление
водорода, МПа (кгс/см2)
|
1,5 (15)
|
2,5 (25)
|
4,9 (50)
|
9,8 (100)
|
19,6 (200)
|
29,4 (300)
|
39,2 (400)
|
20,
22К, 15ГС, 16ГС, 09Г2С
|
290
|
280
|
260
|
230
|
210
|
200
|
190
|
14ХГС
|
310
|
300
|
280
|
260
|
250
|
240
|
230
|
30ХМА
|
400
|
390
|
370
|
330
|
290
|
260
|
250
|
20Х2М
|
480
|
460
|
450
|
430
|
400
|
390
|
380
|
15Х2МФА
18Х2МФА
25Х2МФА
|
510
|
490
|
460
|
420
|
390
|
380
|
380
|
22Х3М,
25Х3МФА
|
510
|
500
|
490
|
475
|
440
|
430
|
420
|
18Х3МФ
|
510
|
500
|
470
|
450
|
20Х3МВФ,
15Х5М, 08X13, 12X13, 20X13, 30X13, 12Х18Н10Т, 10Х17Н13М2Т, 10Х17Н13М3Т,
08Х17Н15М3Т
|
510
|
Примечания: 1. Максимально
допустимые температуры применения в водородосодержащих средах приняты не выше
температур, установленных обязательным приложением 1.
2. Параметры применения
сталей, указанные в таблице, относятся также к сварным соединениям при
условии, если легирование металла шва не ниже, чем основного металла.
|
(Новая
редакция, Изм. № 2).
Таблица 2
Максимально допустимые парциальные давления
окиси углерода МПа (кгс/см2)
Тип стали
|
Температура, °С
|
до 100
|
свыше 100
|
Углеродистые
и низколегированные с содержанием хрома до 2 %
|
23,5 (240)
|
-
|
Низколегированные
с содержанием хрома свыше 2 до 5 %
|
9,8 (100)
|
Хромистые
коррозионностойкие стали ферритного класса с содержанием хрома 13 %
|
13,7 (140)
|
Коррозионностойкие
стали аустенитного класса
|
23,5 (240)
|
Примечание.
Условия применения установлены для скорости карбонильной коррозии не более
0,5 мм/год
|
(Новая
редакция, Изм. № 2).
Таблица 3
Максимально допустимые температуры применения
сталей в средах, содержащих аммиак (°С)
Марки стали
|
Парциальное давление
аммиака, МПа (кгс/см2)
|
св. 0,98 до 1,96 (св. 10
до 20)
|
св. 1,96 до 4,90 (св. 20
до 50)
|
св. 4,90 до 7,84 (св. 50 до 80)
|
20,
22К, 15ГС, 16ГС, 09Г2С
|
300
|
14ХГС,
30ХМА
|
340
|
330
|
310
|
20Х2М,
22Х3М, 15Х2МФА, 18Х2МФА, 25Х2МФА, 25Х3МФА, 18Х3МВ, 20Х3МВФ, 15Х5М, 08X13,
12X13, 20X13, 30X13
|
360
|
350
|
340
|
12Х18Н10Т,
10Х17Н13М2Т, 10Х17Н13М3Т, 08Х17Н15М3Т
|
510
|
Примечание.
Условия применения установлены для скорости азотирования не более 0,5 мм/год.
|
(Новая
редакция, Изм. № 2).
Справочное
Таблица
Марка
стали
|
Вид
термообработки
|
Температура
нагрева, °С
|
Охлаждающая
среда
|
20
|
Нормализация или закалка
|
860
- 920
|
воздух, вода, масло
|
Отпуск
|
650
- 680
|
воздух
|
22К
|
Нормализация или закалка
|
880
- 920
|
воздух, вода, масло
|
Отпуск
|
600
- 700
|
вода
|
15ГС
|
Нормализация или закалка
|
900
- 930
|
воздух, масло, вода
|
Отпуск
|
540
- 560
|
масло, вода
|
09Г2С
|
Закалка
|
910
- 930
|
масло
|
Отпуск
|
640
- 660
|
масло, вода
|
14ХГС
|
Закалка
|
900
- 930
|
вода, масло
|
Отпуск
|
540
- 560
|
вода, масло
|
30ХМА
|
Закалка
|
850
- 880
|
масло, вода
|
Отпуск
|
660
- 680
|
масло, вода
|
20Х2МА
|
Нормализация или закалка
|
900
- 920
|
воздух, масло
|
Отпуск
|
650
- 670
|
воздух
|
22Х3М
|
Нормализация или закалка
|
890
- 910
|
воздух, масло
|
Отпуск
|
650
- 680
|
воздух
|
18Х3МВ
|
Закалка
|
950
- 970
|
масло
|
Отпуск
|
660
- 690
|
воздух
|
20Х3МВФ
|
Закалка
|
1000
- 1020
|
масло
|
Отпуск
|
660
- 690
|
масло
|
15Х2МФА
18Х2МФА
|
Закалка
|
1000
|
масло
|
25Х2МФА
25Х3МФА
|
Отпуск
|
650
- 690
|
масло
|
38ХН3МФА
|
Закалка
|
860
- 880
|
масло
|
Отпуск
|
650
- 670
|
масло
|
08X13
|
Закалка
|
1000
- 1050
|
воздух, масло
|
Отпуск
|
700
- 800
|
масло
|
12X13
|
Закалка
|
1000
- 1050
|
воздух, масло
|
Отпуск
|
700
- 790
|
масло
|
20X13
30X13
|
Закалка
|
1000
- 1050
|
воздух
|
Отпуск
|
700
- 780
|
масло
|
12Х18Н10Т
10Х17Н13М2Т
10Х17Н13М3Т
06Х17Н15М3Т
|
Закалка
|
1050
- 1100
|
вода, масло
|
16ГС
|
Нормализация
|
900
- 930
|
воздух
|
Отпуск
|
620
- 680
|
воздух
|
15Х5М
|
Нормализация
|
950
- 980
|
воздух
|
Отпуск
|
840
- 880
|
воздух
|
(Измененная
редакция, Изм. № 2).
Обязательное
Таблица
Марка стали
|
Толщина, мм
|
Предел текучести, σ0,2
|
Временное сопротивление
разрыву, σв
|
Относительное удлинение,
δ5
|
Относительное сужение,
φ
|
Ударная вязкость, ан,
кДж/м2 (кгс·м/см2)
|
Твердость по Бринеллю НВ
|
ГОСТ или ТУ
|
МПа (кгс/мм2)
|
%
|
не менее
|
20
|
до 300
|
196 (20)
|
392 (40)
|
20
|
-
|
500 (5)
|
123 - 167
|
По ГОСТ
22790-83
|
301 - 500
|
167 (17)
|
334 (34)
|
15
|
34
|
400 (4)
|
103 - 148
|
По ГОСТ
8479-70
|
501-800
|
167 (17)
|
334 (34)
|
14
|
30
|
360 (3,5)
|
103 - 148
|
22К
|
до 500
|
216 (22)
|
432 (44)
|
15
|
39
|
400 (4)
|
123 - 167
|
По ТУ 24-3-15-865-75
|
15ГС
|
до 350
|
294 (30)
|
490 (50)
|
18
|
-
|
600 (6)
|
149 - 207
|
По
ГОСТ
22790-77
|
09Г2С
|
до 500
|
294 (30)
|
451 (46)
|
24
|
45
|
600 (6)
|
120 - 179
|
По настоящему стандарту
|
14ХГС
|
до 550
|
314 (32)
|
490 (50)
|
17
|
-
|
600 (6)
|
149 - 207
|
По ГОСТ
22790-83
|
30ХМА
|
до 350
|
392 (40)
|
589 (60)
|
16
|
-
|
600 (6)
|
197 - 241
|
По ГОСТ
22790-83
|
20X2МА
|
до 550
|
392 (40)
|
539 (55)
|
16
|
-
|
600 (6)
|
197 - 235
|
По ГОСТ
22790-83
|
22Х3М
|
до 550
|
441 (45)
|
589 (60)
|
16
|
50
|
600 (6)
|
197 - 235
|
По ТУ 108-838-79
|
551 - 700
|
392 (40)
|
539 (55)
|
16
|
45
|
600 (6)
|
174 - 217
|
15Х2МФА
(48ТС-3-40)
|
161
- 400
|
432 (44)
|
539 (55) - 736 (75)
|
11
|
40
|
300 (3)
|
187 - 229
|
ПО ТУ 108.131-75
|
18Х2МФА
(48ТС-3)
|
530 (54)
|
638 (65) - 834 (85)
|
11
|
40
|
250 (2,5)
|
207 - 225
|
25Х2МФА
(48ТС-1)
|
до 450
|
432(44)
530(54)
|
539 (55)
636 (65)
|
11
11
|
40
40
|
300 (3)
250 (2,5)
|
187 - 229
207 - 225
|
25Х3МФА
(48ТС-4)
|
до 600
|
432 (44)
530 (54)
|
539 (55)
638 (65)
|
11
11
|
40
40
|
300 (3)
250 (2,5)
|
187 - 229
207 - 225
|
18Х3МФА
|
до 350
|
441 (45)
|
589 (60)
|
16
|
-
|
600 (6)
|
197 - 241
|
По ГОСТ
22790-83
|
20Х3МВФ
|
до 350
|
667 (68)
|
784 (80)
|
14
|
-
|
600 (6)
|
241 - 285
|
38ХН3МФА
|
до 450
|
638 (65)
|
784 (80)
|
13
|
35
|
600 (6)
|
-
|
По
настоящему стандарту
|
08X13
|
до 50
|
-
|
-
|
-
|
-
|
-
|
187 - 229
|
По
ГОСТ
25054-81
|
12X13
|
до 50
|
-
|
-
|
-
|
-
|
-
|
187 - 229
|
20X13
|
до 200
|
-
|
-
|
-
|
-
|
-
|
197 - 248
|
30X13
|
до 200
|
-
|
-
|
-
|
-
|
-
|
235 - 277
|
12Х18H10Т
|
до 500
|
196 (20)
|
490 (50)
|
35
|
-
|
-
|
-
|
ГОСТ
25054-81
|
12Х18Н10Т
10Х17Н13М2Т
10Х17Н13М3Т
08Х17Н15М3Т
|
до 350
|
По ГОСТ
22790-83
|
16ГС
|
до
400
|
274 (28)
|
451 (46)
|
14
|
38
|
39 (4,0)
|
120 - 179
|
ОСТ
108.030.113-77
|
15Х5М
|
до
400
|
216 (22)
|
392 (40)
|
22
|
50
|
118 (12)
|
не более 170
|
ГОСТ
20072-74
|
Примечания:
1. Максимальная масса поковок указана в справочном приложении 6.
2. У стали марок 15Х2МФА, 18Х2МФА, 25Х2МФА,
25Х3МФА данные ударной вязкости приведены для образцов типа II ГОСТ
9454-78 (СТ
СЭВ 472-77, СТ СЭВ 473-77).
3. Стали 08Х13, 12Х13,
20Х13, 30X13 применяются для изготовления уплотнительных колец.
|
|
|
|
|
|
|
|
|
|
|
(Измененная
редакция, Изм. № 1, 2).
Обязательное
Таблица
Марка
стали
|
Стандарт
или технические условия
|
Нормативные
прочностные характеристики при 20 °С
|
Предел
текучести σ0,2,
МПа (кгс/мм2)
|
Временное
сопротивление разрыву σв, МПа (кгс/мм2)
|
σ0,2
|
σв
|
Температура,
°С
|
МПа
(кгс/мм2)
|
100
|
150
|
200
|
250
|
300
|
350
|
400
|
450
|
500
|
100
|
150
|
200
|
250
|
300
|
350
|
400
|
450
|
500
|
20
|
ГОСТ
8479-70
|
167 (17,0)
|
334 (34,0)
|
167 (17,0)
|
162 (16,5)
|
157 (16,0)
|
147 (15,0)
|
137 (14,0)
|
128 (13,0)
|
108 (11,0)
|
98 (10,0)
|
-
|
334 (34,0)
|
329 (33,5)
|
314 (32,0)
|
304 (31,0)
|
294 (30,0)
|
284 (29,0)
|
275 (38,0)
|
343 (35,0)
|
-
|
ГОСТ
22790-83
|
196 (20,0)
|
432 (44,0)
|
196 (20,0)
|
191 (19,5)
|
186 (19,0)
|
172 (17,5)
|
157 (16,0)
|
137 (14,0)
|
118 (12,0)
|
-
|
-
|
432 (44,0)
|
427 (43,5)
|
422 (43,0)
|
412 (42,0)
|
397 (40,5)
|
383 (39,0)
|
368 (37,5)
|
-
|
-
|
22К
|
По настоящему стандарту
|
216 (22,0)
|
432 (44,0)
|
216 (22,0)
|
206 (21,0)
|
196 (20,0)
|
191 (19,5)
|
186 (19,0)
|
182 (18,5)
|
167 (17,0)
|
-
|
-
|
432 (44,0)
|
412 (42,0)
|
392 (40,0)
|
383 (39,0)
|
373 (38,0)
|
373 (38,0)
|
363 (37,0)
|
-
|
-
|
15ГС
|
ГОСТ 22790-83
|
294 (30,0)
|
490 (50,0)
|
294 (30,0)
|
284 (29,0)
|
275 (28, 0)
|
245 (25,0)
|
226 (23,0)
|
196 (20,0)
|
167 (17,0)
|
-
|
-
|
451 (46,0)
|
451 (46, 0)
|
441 (45,0)
|
432 (44,0)
|
412 (42,0)
|
402 (41,0)
|
392 (40,0)
|
-
|
-
|
09Г2С
|
По настоящему стандарту
|
294 (30,0)
|
451 (46,0)
|
280 (28,5)
|
270 (27,5)
|
255 (26,0)
|
235 (24,0)
|
206 (21,0)
|
196
(20,0)
|
186 (19,0)
|
-
|
-
|
441 (45,0)
|
437 (44,5)
|
432 (44,0)
|
412 (42,0)
|
383 (39,0)
|
378 (38,5)
|
373 (38,0)
|
-
|
-
|
14ХГС
|
ГОСТ
22790-83
|
314 (32,0)
|
490 (50,0)
|
294 (30,0)
|
284 (29,0)
|
275 (28,0)
|
265 (27,0)
|
255 (26,0)
|
245 (25,0)
|
226 (23,0)
|
-
|
-
|
466 (47,5)
|
456 (46,5)
|
441 (45,0)
|
432 (44,0)
|
422 (43,0)
|
412 (42,0)
|
392 (40,0)
|
-
|
-
|
30ХМА
|
ГОСТ
22790-83
|
392 (40,0)
|
589 (60,0)
|
373 (38,0)
|
373 (38,0)
|
363 (37,0)
|
343 (35,0)
|
334 (34,0)
|
334 (34,0)
|
324 (33,0)
|
294 (30,0)
|
245
(25,0)
|
569 (58,0)
|
549 (56,0)
|
540 (55,0)
|
530 (54,0)
|
510 (52,0)
|
490 (50,0)
|
481 (49,0)
|
461 (47,0)
|
412 (42,0)
|
16ГС
|
ОСТ
108.030.113-77
|
275 (280)
|
451 (46,0)
|
275 (28,0)
|
265 (27,0)
|
255 (26,0)
|
245 (25,0)
|
226 (23,0)
|
196 (20,0)
|
167 (17,0)
|
-
|
-
|
451 (46,0)
|
451 (46,0)
|
441 (45,0)
|
432 (44,0)
|
412 (42,0)
|
402 (41,0)
|
392 (40,0)
|
-
|
-
|
15Х5М
|
ГОСТ
20072-74
|
216 (22,0)
|
392 (40,0)
|
206 (21,0)
|
196 (20,0)
|
186 (19,0)
|
182 (18,5)
|
177 (18,0)
|
172 (17,5)
|
167 (17,0)
|
162 (16,5)
|
142 (14,5)
|
373 (38,0)
|
348 (35,5)
|
324 (33,0)
|
319 (32,5)
|
314 (32,0)
|
309 (31,5)
|
304 (31,0)
|
284 (29,0)
|
245 (25,0)
|
20Х2МА
|
ГОСТ
22790-83
|
392 (40,0)
|
539 (55,0)
|
378 (38,5)
|
363 (37,0)
|
348 (35,5)
|
334 (34,0)
|
304 (31,0)
|
289 (29,5)
|
260 (26,5)
|
240 (24,5)
|
216 (22,0)
|
520 (53,0)
|
510 (52,0)
|
500 (51,0)
|
476 (48,5)
|
452 (46,0)
|
432 (44,0)
|
402 (41,0)
|
383 (39,0)
|
358 (36,5)
|
22Х3М
|
ТУ 108-838-79
ГОСТ
22790-83
|
441 (45,0)
|
589 (60,0)
|
417 (42,5)
|
407 (41,5)
|
392 (40,0)
|
373 (38,0)
|
343 (35,0)
|
324 (33,0)
|
294 (30,0)
|
270 (27,5)
|
241 (25,0)
|
569 (58,0)
|
554 (56,5)
|
540 (55,5)
|
520 (53,0)
|
490 (50,0)
|
471 (48,0)
|
441 (45,0)
|
412 (42,0)
|
392 (40,0)
|
ТУ 108-838-79
|
392 (40,0)
|
539 (55,0)
|
373 (38,0)
|
358 (36,5)
|
343 (35,0)
|
319 (32,5)
|
294 (30,0)
|
270 (27,5)
|
245 (25,0)
|
221 (22,5)
|
196 (20,0)
|
525 (53,5)
|
510 (52,0)
|
490 (50,0)
|
466 (47,5)
|
441 (45,0)
|
407 (42,5)
|
392 (40,0)
|
368 (37,5)
|
334 (34,0)
|
15Х2МФА
25Х2МФА
25Х3МФА
|
ТУ 108.131-75
|
432 (44,0)
|
539 (55,0)
|
422 (43,0)
|
417 (42,5)
|
412 (42,0)
|
402 (41,0)
|
397 (40,5)
|
392 (40,0)
|
368 (37,5)
|
343 (35,0)
|
-
|
540 (55,0)
|
530 (54,0)
|
520 (53,0)
|
510 (52,0)
|
500 (51,0)
|
490 (50,0)
|
471 (48,0)
|
441 (45,0)
|
-
|
18Х2МФА
25Х2МФА
25Х3МФА
|
530 (54,0)
|
638 (65,0)
|
520 (53,0)
|
515 (52,5)
|
510 (52,0)
|
500 (51,0)
|
495 (50,5)
|
490 (50,0)
|
451 (46,0)
|
422
(43,0)
|
-
|
618 (63,0)
|
598 (61,0)
|
589 (60,0)
|
569 (58,0)
|
559 (57,0)
|
549 (56,0)
|
520 (53,0)
|
490 (50,0)
|
-
|
18Х3МФ
|
ГОСТ 22790-83
|
441 (45,0)
|
589 (60,0)
|
427 (43,5)
|
417 (42,5)
|
392 (40,0)
|
383 (39,0)
|
373 (38,0)
|
363 (37,0)
|
343 (35,0)
|
304 (31,0)
|
275 (28,0)
|
564 (57,5)
|
549 (56,0)
|
540 (55,0)
|
525 (53,5)
|
515 (52,5)
|
500 (51,0)
|
490 (50,0)
|
461 (47,0)
|
402 (41,0)
|
20Х3МВФ
|
ГОСТ
22790-83
|
667 (68,0)
|
784 (80,0)
|
648 (66,0)
|
633 (64,5)
|
618 (63,0)
|
598 (61,0)
|
589 (60,0)
|
579 (59,0)
|
569 (58,0)
|
530 (54,0)
|
500 (51,0)
|
746 (76,0)
|
731 (74,5)
|
716 (73,0)
|
687 (70,0)
|
677 (69,0)
|
657 (67,0)
|
638 (65,0)
|
608 (62,0)
|
559 (57,0)
|
38ХН3МФА
|
По настоящему стандарту
|
638 (65,0)
|
784 (80,0)
|
618 (63,0)
|
598 (61,0)
|
579 (59,0)
|
569 (58,0)
|
564 (57,5)
|
559 (57,0)
|
549 (56,0)
|
540 (55,0)
|
-
|
736 (75,0)
|
721 (73,5)
|
706 (72,0)
|
706 (72,0)
|
697 (71,0)
|
687 (70,0)
|
667 (68,0)
|
608 (62,0)
|
-
|
08X13
|
ОСТ 26-704-72
|
373 (38,0)
|
559 (57,0)
|
373 (38,0)
|
353 (36,0)
|
334 (34,0)
|
329 (33,5)
|
324 (33,0)
|
319 (32,0)
|
298 (30,0)
|
284 (29,0)
|
275 (28,0)
|
539 (55,0)
|
520 (53,0)
|
500 (51,0)
|
495 (50,5)
|
490 (50,0)
|
471 (48,0)
|
453 (46,0)
|
402 (41,0)
|
353 (36,0)
|
12X13
|
373 (38,0)
|
589 (60,0)
|
373 (38,0)
|
353 (36,0)
|
334 (34,0)
|
329 (33,5)
|
324 (33,0)
|
318 (32,5)
|
319 (32,0)
|
304 (31,0)
|
275 (28,0)
|
589 (60,0)
|
559 (57,0)
|
539 (55,0)
|
539 (55,0)
|
539 (55,0)
|
525 (53,5)
|
510 (52,0)
|
490 (50,0)
|
333 (39,0)
|
20X13
|
471 (48,0)
|
628 (64,0)
|
451 (46,0)
|
432 (44,0)
|
417 (42,0)
|
392 (40,0)
|
363 (37,0)
|
363 (37,0)
|
363 (37,0)
|
343 (35,0)
|
324 (33,0)
|
589 (60,0)
|
549 (56,0)
|
530 (54,0)
|
510 (52,0)
|
490 (50,0)
|
476 (48,5)
|
461 (47,0)
|
432 (44,0)
|
363 (37,0)
|
30X13
|
559 (57,0)
|
696 (71,0)
|
539 (55,0)
|
530 (54,0)
|
520 (53,0)
|
510 (52,0)
|
500 (51,0)
|
461 (47,0)
|
441 (45,0)
|
427 (43,0)
|
417 (42,0)
|
667 (68,0)
|
657 (67,0)
|
657 (67,0)
|
642 (65,5)
|
628 (64,0)
|
598 (61,0)
|
569 (58,0)
|
549 (56,0)
|
530 (54,0)
|
12Х18Н10Т
10Х17Н13М2Т
10Х17Н13М3Т
08Х17Н15М3Т
|
ГОСТ
22790-83
|
196 (20,0)
|
490 (50,0)
|
186 (19,0)
|
177 (18,0)
|
172 (17,5)
|
167 (17,0)
|
157 (16,0)
|
152 (15,5)
|
147 (15,0)
|
142 (14,5)
|
132 (13,5)
|
-
|
-
|
-
|
-
|
-
|
-
|
-
|
-
|
-
|
Примечание. Прочностные
характеристики при промежуточных температурах допускается определять методом линейной
интерполяции
|
(Измененная
редакция, Изм. № 2).
Справочное
Таблица
Марка
стали
|
Максимальная
масса поковок, т
|
20
|
65
|
22К
|
65
|
15ГС
|
3
|
09Г2С
|
3
|
14ХГС
|
3
|
30ХМА
|
3
|
20Х2МА
|
6,2
|
22Х3М
|
85
|
18Х3МВ
|
5
|
20Х3МВФ
|
5
|
15Х2МФА
|
85
|
18Х2МФА
|
85
|
25Х2МФА
|
85
|
25Х3МФА
|
85
|
38ХН3МФА
|
85
|
08X13
|
3
|
12X13
|
3
|
20X13
|
3
|
30X13
|
3
|
12Х18Н10Т
|
5
|
10Х17Н13М2Т
|
5
|
10Х17Н13М3Т
|
5
|
08Х17Н15М3Т
|
5
|
Техническое управление
|
|
Зам. начальника
ВПО Союзхиммаш
|
В.Н. Иванов
|
И.о. начальника
ИркутскНИИхиммаш
|
Ю.Б. Рехлов
|
Директор
|
В.Г. Усенко
|
Заместитель
директора
|
Е.Р. Хисматулин
|
Заведующий отделом
стандартизации
|
В.И. Королев
|
Заведующий отделом
№ 11
|
В.Д. Молчанова
|
Руководитель темы,
заместитель заведующего отделом
|
Г.Г. Золотенин
|
Старший инженер
|
Т.П. Бурдуковская
|
Заведующий
лабораторией отдела № 7
|
В.И. Этингов
|
Старший инженер
|
Л.А. Корчагина
|
СОГЛАСОВАНО
|
|
НИИхиммаш
|
|
И.О. Директора
|
|
Заместитель
директора
|
П.Ф. Серб
|
Начальник ВНИОС
|
В.В. Дюкин
|
ПО Уралхиммаш
|
|
Главный инженер
|
Н.К. Глобин
|
ЛИСТ ССЫЛОЧНЫХ
ДОКУМЕНТОВ
Обозначение
|
Наименование
|
ГОСТ
1050-74
|
«Сталь
углеродистая качественная, конструкционная».
|
ГОСТ
19282-73
|
«Сталь
низкоуглеродистая толстолистовая и широкополосная универсальная».
|
ГОСТ
4543-71
|
«Сталь
легированная конструкционная».
|
ГОСТ 20072-74
|
«Сталь
теплоустойчивая».
|
ГОСТ
5632-72
|
«Стали
высоколегированные и сплавы коррозионностойкие, жаростойкие и жаропрочные».
|
ГОСТ
8479-70
|
«Поковки
из конструкционной углеродистой и легированной стали».
|
ГОСТ
22790-77
|
«Сборочные
единицы и детали трубопроводов на Ру св. 9,81 до
98,1 МПа (св. 100 до 1000 кгс/см2)».
|
ОСТ 108.030.113-77
|
«Поковки
из углеродистой легированной и высоколегированной сталей для котлов, сосудов
и станционных трубопроводов. Общие технические условия».
|
ОСТ 26-704-72
|
«Поковки
из коррозионностойких сталей для химического и нефтеперерабатывающего
машиностроения. Общие технические условия».
|
ТУ 24-3-15-865-75
|
«Поковки
из стали марки 22Х3М для сосудов высокого давления»
|
ТУ 108.131-75
|
«Заготовки
из теплоустойчивой стали».
|
ГОСТ
7829-70
|
«Поковки
из углеродистой и легированной стали, изготовляемые свободной ковкой на
молотах. Припуски и допуски».
|
ГОСТ
7062-79
|
«Поковки
из углеродистой и легированной стали, изготовляемые ковкой на прессах.
Припуски и допуски».
|
ГОСТ
12344-78 - ГОСТ
12365-78
|
«Стали
легированные и высоколегированные. Методы химического анализа».
|
ГОСТ
18442-80
|
«Контроль
неразрушающий. Капиллярные методы. Общие требования».
|
ГОСТ
21105-75
|
«Контроль
неразрушающий. Магнитопорошковый метод».
|
ГОСТ
24507-80
|
«Контроль
неразрушающий. Поковки из черных и цветных металлов. Методы ультразвуковой
дефектоскопии».
|
ГОСТ
2789-73 (СТ СЭВ 638-77)
|
«Шероховатость
поверхности. Параметры и характеристики».
|
ГОСТ 1497-84
|
«Металлы.
Методы испытания на растяжение».
|
ГОСТ
9454-78 (СТ СЭВ 472-77, СТ СЭВ 473-77)
|
«Металлы.
Методы испытаний на ударный изгиб при пониженной, комнатной и повышенной
температурах».
|
ГОСТ
9012-59 (СТ СЭВ 468-77)
|
«Металлы.
Методы испытаний. Измерение твердости по Бринеллю».
|
ГОСТ
1778-70 (СТ СЭВ 4077-83)
|
«Сталь.
Металлографические методы определения неметаллических включений».
|
ГОСТ
6032-84 (СТ СЭВ 4076-83)
|
«Стали
и сплавы коррозионностойкие. Методы определения стойкости против
межкристаллитной коррозии».
|
(Измененная
редакция, Изм. № 2).
СОДЕРЖАНИЕ
|